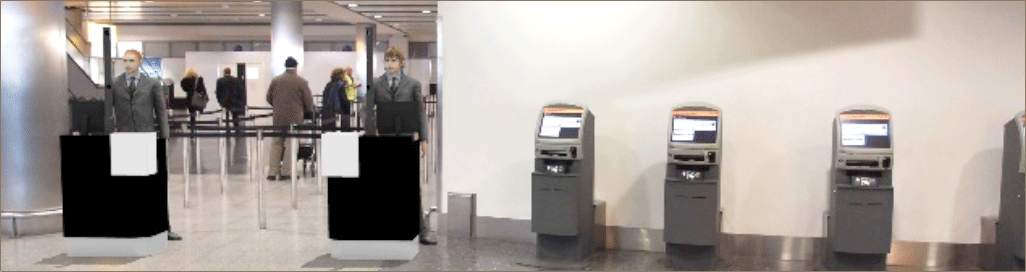
news & blog
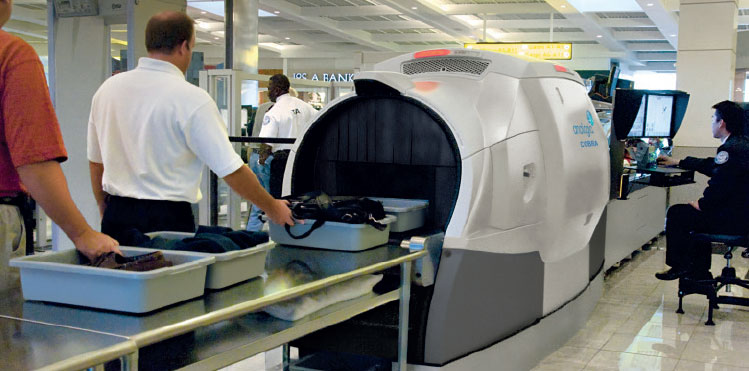
BLOG: Integrating new equipment into passenger screening operations
17th October 2019
Those working in a passenger screening environment will be accustomed to adapting to change. Over the past 5 years alone we have seen the introduction of new liquids screening regulations, ETD and body scanning technologies and, currently, the emergence of computed tomography (CT) security equipment. These are in addition to the changes that individual airports choose to make in the interest of performance and customer service, for example extended preparation benches and automated tray return.
With new equipment come new processes, work methods and instructions to passengers and, as a result, changes in how an operation performs. This may mean slower production rates which, if not planned for and managed, can lead to longer waiting times and a negative impact on service. New equipment can indeed increase throughput; to reap the full benefit it is necessary for all elements of an end-to-end process to be able to operate to the same level of throughput, otherwise the overall benefit is lost.
So how do you know which technology, or combination of equipment, is right for your airport? Naturally the high capital investment involved in installing new equipment airport-wide often leads to budget led choices. However, cost aside, the most effective way of identifying an appropriate solution for your airport should be based on a period of research, testing and trialling. There is great value in understanding how different equipment types work in a live operating environment in your airport with your passenger profile, capitalising on the experience of your operations team. Conducting these assessments in a measured, controlled manner will ensure you get the most out of this exercise.
Making the appropriate choice of equipment is just the first step; ensuring that the solution will work long-term and achieve an expected level of performance across your airport is the next. Effective integration requires an understanding of the whole passenger security process; how each element of the process performs and affects the subsequent step, and particularly how the new equipment will change the dynamics of the current operation.
With a detailed understanding of the CONOPs of the chosen equipment, any adaptations of the screening process need to ensure that security regulations and health and safety guidelines are fully respected while creating a streamlined operation. Working closely with airport operations teams to test changes in live operation helps to achieve this, as well as gaining valuable feedback from experienced staff. It is important to routinely review the process during the testing and trial phases to identify additional opportunities for improvement and ultimately get the best out of the new investment.
Maximising the performance of the new technology and, at the same time, the end-to-end process requires effective training and clear communications. Providing instructions and coaching that are fully understood and employed consistently by all staff members will make the implementation phase much easier and help to achieve predictable performance across the airport, rather than variations depending on who is on duty and which terminal you are in.
This goes hand-in-hand with instilling a culture of continual improvement; where supervisors and management are encouraged to identify when the operation is not performing to the level it can and what may be causing this. Whether the issue lies in the process itself or a change in passenger profile or volumes, addressing it will enable the airport to continue to make best use of its new and existing assets.
o&i consulting has extensive experience of helping airport operators to successfully identify and implement new equipment and processes. The attached flyer provides more information on our expertise in this area. We also invite you to contact us at: clairemorgan@oandiconsulting.com
Categories: Blogs, Passenger Security Screening
Tags: airport security, aviation security, CT, equipment integration, ETD, LAGS, passenger screening, passenger security